Metal alloys have been around for a long time. Silver and gold sometimes get mixed up to make electrum and meteorites provide us with a celestial mix of iron and nickel. The first man-made alloy was bronze made from a mix of tin and copper. Things have come a long way since the bronze age.
IBC Advanced Alloys Corp. (IB: TSX-V or IAALF: OTCQX) is combining copper or beryllium with other elements to produce specialized metals alloys for a range of applications. The aerospace and automotive industries in particular are keen to find metals that will provide high performance characteristics. Extreme temperature tolerance, durability, ruggedness, flexibility are just a few of the distinctions manufacturers need for large, high-value final products. Increasingly, energy efficiency and fuel economy are driving forces behind design decisions.
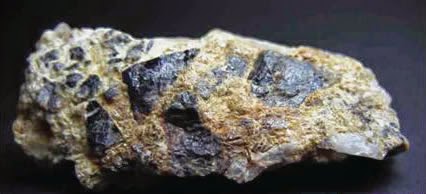
Both automotive and aerospace manufacturers have been using steel, aluminum and more recently carbon composites for various parts and components of their airplanes and cars. Weight performance and cost considerations have long governed engineering choices for one metal solution or another in the aerospace industry. Now too automotive engineers are experiencing the pressure of emissions regulations called the
CAFE standards. Auto OEMS are finding weight reduction through lighter metals just as effective as alternative fuels and modified propulsion systems. Demand conditions could not be better for a young company to commercialize smart, innovative metal alloy technology.
IBC has gained some traction in the market for specialized metals. The company just formed a partnership with Baoshida Swissmetal Ltd. and Avins USA, Inc. to manufacture a copper alloy. IBC expects the alloy could have applications in multiple markets with potential for as much as $10 million in revenue for the partnership over the next three years.
Even more exciting is a contract with Lockheed Martin to supply cast components for the electro-optical targeting system for the
F-35 Lighting II stealth fighter aircraft. IBC will be casting these components using its proprietary beryllium-aluminum alloy. The first shipments to Lockheed for the azimuth gimbal housing will go out the door yet in 2014., under a low-volume contract valued at $2.0 million. IBC management has high confidence the company will be tapped to provide cast components for other parts of the F-35 electro-optical targeting system.
IBC calls their metal alloy ‘Beralcast.’ Since it represents the first ‘cast’ beryllium metal alloy they are confident Lockheed and others will be ringing IBC’s phone. When added to other elements such as aluminum, copper or iron, beryllium significantly improves physical characteristics. The resulting alloy is stronger, harder and lighter. However, until IBC came along, beryllium alloys were typically stamped in a press, limiting design options and lengthening production times. A cast beryllium alloy opens the door to many applications that might otherwise require engineers to compromise on performance or cost with other metals.
The company reported $16.9 million in sales in its fiscal year ending June 2014, mostly from its copper alloy division. This was well below sales in the previous fiscal year and reveals one of the greatest frustrations with highly innovative industrial companies like IBC Advanced Alloys. No matter how smart their engineers might be, relationships with industrials are still long in development. Work is often related to a large project involving a prime contract and a distant end-user. Such projects can be subject to false starts and delays. That means revenue can be variable and might not be easily predicted.
On the plus side in the last fiscal year, the mix of business delivered a stronger gross profit margin of 8.1% compared to 7.0% on higher revenue in the previous year. That meant that the operating loss was lower compared to last year. Even so operations required $2.1 million in cash to keep things the works going mostly for working capital purposes. IBC had $1.5 million in cash on its balance sheet at the end of June 2014, providing the company with something of a cushion to start up production for Lockheed Martin’s order.
IBC’s progress in taking its metal alloys to the marketplace does not seem to be registered in the stock price as yet. At just a few pennies per share, the stock is more like a cheap option on management’s ability to execute on the business plan. Book value per share is $0.13, just one penny more than the stock price. Most of IBC’s assets are composed of raw materials, property, plant and equipment. There is outstanding debt on IBC’s balance sheet through lines of credit, but likely the value of the company’s hard assets exceed book value and provide excellent collateral.
In my view, there is more to the company than is reflected in the stock price. Yet it is clear that an investment in IBC Advanced Alloys will require patience and a tolerance for risk and volatility. For the less patient, this company is still worth putting on a watch list for the next and perhaps less risky chapter in its development.
The author of this article has a long position in IAALF shares