In October 2015, I paid a visit to the Coosa graphite project in the USA, being developed by Alabama Graphite Corp. (TSX.V:ALP, OTCQX:ABGPF) in Coosa County, Alabama.
Located in a past-producing region of the state known as the Alabama Graphite Belt, the Coosa project is approximately 50 miles south-southeast of Birmingham and 20 miles north of Montgomery. The project is also 30 miles northeast of the Bama Mine project, also owned by Alabama Graphite Corp. (AGC).
20 miles to the northeast, AGC has its field office and core storage facility in Sylacauga, which I also had the chance to visit. Sylacauga is home to the world's largest marble quarry, and the source of the pure, white marble used in the construction of many famous buildings and memorials in the USA, including the US Supreme Court building, the US Capitol rotunda and the Lincoln Memorial in Washington, DC.
I was hosted during my visit by Don Baxter, President & CEO of AGC, Rick Keevil, VP for Project Development and Jesse Edmondson, Project Geologist for Coosa and also Director of Community Relations.
Per the October 2015 NI 43-101 guided mineral-resource estimate for the Coosa deposit, at a 1% graphitic carbon (Cg) cut-off grade, 78.5 megatonnes (Mt) of the resource is at the Indicated level @ 2.39% Cg and 79.4 Mt is at the Inferred level @ 2.56% Cg. This results in an estimated 3.9 Mt of Cg present in the mineral resource at Coosa. The resource estimate was based on the results of 109 drill holes totaling 7,900 m (25,900 feet) and 9 trenches totaling 1,150 m (3,800 feet).
Graphite development companies typically report on the distribution of flake sizes in their graphite deposits. Metallurgical results announced by the company in May 2015, and subsequently reported in the PEA report indicate that approximately 25-30% of the graphite present at Coosa is in the form of large flakes (+80 mesh or >180 μm). However, as we will see later in this article, AGC's intended approach to production potentially negates the need for significant quantities of large-flake graphite to be present in the deposit, since the company's plan is to process graphite across the range of flake sizes, into higher-value engineered graphite products.
You can see photographs taken during the visit in the galleries below.
The name of the Coosa project has its roots in the local history of the area. Historically, Coosa was a Native American province, which included parts of present-day Alabama, Georgia, Tennessee, and South Carolina. This province gave its name to the Coosa River, which flows at the western boundary of Coosa County. The area is situated towards the southern end of the Appalachian mountain range, in the Northern Piedmont geological province.
AGC holds the mineral rights to a total of 17,000 ha (42,000 acres) of land at and around the Coosa project location. Mr. Baxter indicated that the surface rights for the Coosa Project are owned by a timber company, and are currently leased by AGC for exploration use. He commented that AGC has an excellent working relationship with this timber company and that they are supportive of the project's continued development.
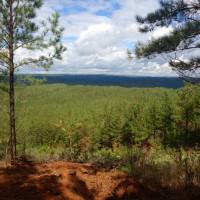
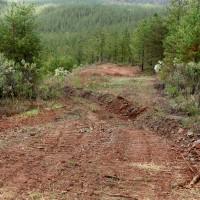
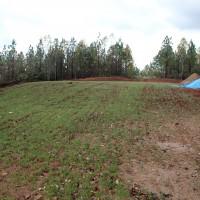
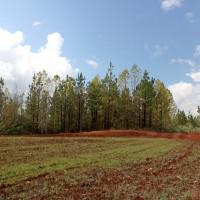
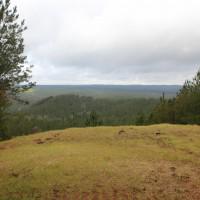
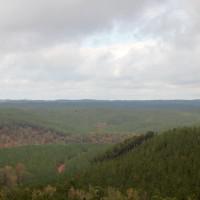
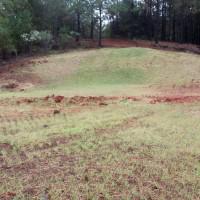
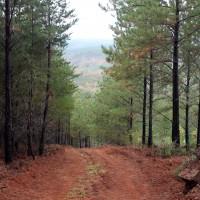

The host formation for the Coosa deposit consists primarily of schists, including quartz-muscovite-biotite-graphite schist, quartz-graphite schist, quartz-biotite-garnet schist and combinations of these. Schists are medium- to coarse-grained rocks, formed through the metamorphosis of shale or igneous rocks. The resulting foliation, or planes of weakness in the rock, makes it relatively straightforward to break up these materials for processing. Mr. Baxter commented that the quartz and other waste minerals that will result from processing these schists, could potentially be sold and used for a variety of end uses, including the production of roof shingles and the like.
Although the project location is rural, the Coosa project is well served by local roads, with interstate highway 65 less than 5 miles from the property. Coosa is close to other local infrastructure, with the nearest town just 5 minutes away from the site.
Mr. Keevil explained that the top 20-30 m (60-100 feet) of the graphite-bearing material at the Coosa deposit has been oxidized and weathered over time, resulting in a very soft rock that is easy to excavate and to process. This was confirmed during the site visit, with on-site sample materials easily crushable by hand. This weathered layer means that for a significant portion of the mine life, no drilling or blasting will be required to obtain the graphite ore; instead simple excavating equipment will be used in an open pit to get at the materials.
With one or two exceptions, junior-mining companies looking to develop graphite projects typically focus on the production of run-of-mine (ROM) concentrates, produced by beneficiating graphite ores using standard processes such as crushing, milling and flotation. ROM concentrates are typically sold directly to end-users in a number of sectors. Given the relatively low value of such materials, projects focused on ROM concentrates likely need to have high head grades in their graphite deposits, to reduce the costs of ROM concentrate production and to generate reasonable margins.
The path to greater revenues (and margins) for any future graphite producer lies in upgrading the ROM concentrate, preferably in-house, so that it can be used to produce the anodes for lithium-ion batteries (LIBs). Battery-grade graphite requires particularly high purity levels, typically greater than 99.9% Cg.
Mr. Baxter explained that the AGC business model is focused on the production of highly engineered graphite, mostly for the production of LIB anodes. Recent initiatives by Tesla Motors (NASDAQ:TSLA) and others to produce large quantities of LIBs for electric vehicles and home energy storage, will require significant quantities of graphite to meet demand. In keeping with the 'green' credentials of such end users, such graphite will need to be produced in jurisdictions that mandate a significant degree of environmental protection, with respect to the methods used to produce engineered graphite products.
During battery operation, in order for the lithium ions in the LIB electrolyte to efficiently diffuse between graphite particles within the anodes, the particles need to be small, and this is achieved through micronization of the precursor graphite powders. Standard battery-grade graphite requires an average diameter of approximately 10-30 μm.
Such materials also need to be spheroidized - increasing the packing or 'tap' density of graphite particles by converting the naturally flat graphite flakes into potato-like shapes. The combination of high purity and tap density enhances the electrical conductivity of the graphite anodes, during use in the LIB.
Conventional wisdom for battery-grade graphite developers, has been to focus on graphite deposits that contain significant proportions of large (>150 μm) graphite flakes, because the purity of the graphite flakes tends to increase with flake size. However, given the additional energy costs required to micronize large flakes, the ideal precursor material would have small flake size, if it had sufficient purity levels (either as-is or through a cost-effective purification process) for the subsequent processing to be economically viable, and if it can be effectively spheroidized.
In addition to micronizing and spheroidizing high-purity graphite, battery-grade powders also need for the individual particles to be coated, typically using a non-graphitic carbon material, to reduce the specific surface area of the powder. Lowering the specific surface area increases the ability of the anode to operate efficiently in the battery in which it will operate, increasing the useful life of the battery. Just as important, it reduces the risk of a runaway chemical reaction, which could lead to a dangerous situation in usage.
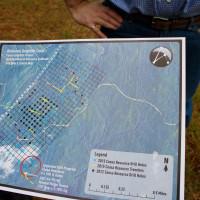
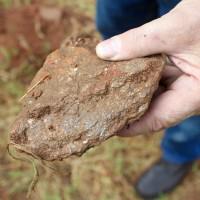
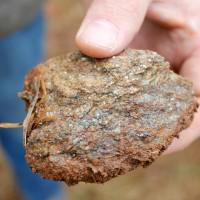
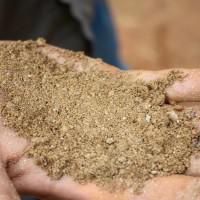
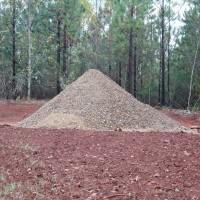
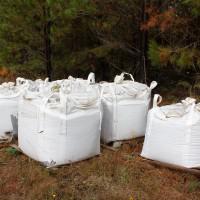
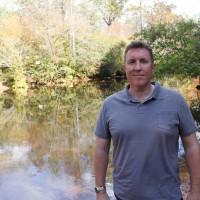
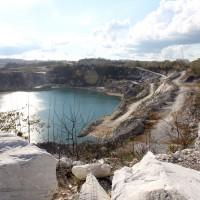
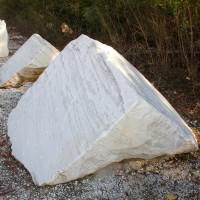
Since Mr. Baxter joined the company in June 2015, AGC has transitioned its business model from that of a potential purveyor of ROM concentrates, to a potential producer of high-purity, engineered graphite. Per the Preliminary Economic Assessment (PEA) for the Coosa project, published in November 2015, AGC intends for 75% of its annual production of graphite to be in the form of coated spherical purified graphite (CSPG), for use in battery anodes, with the remaining 25% of production being sold as purified micronized graphite (PMG), for use in a variety of non-battery applications such as powder metallurgy, friction materials, and polymer, plastic and rubber composites.
Mr. Baxter indicated that the proportions of graphite going into each of the two products is related to the particle sizes that result from micronizing and spheroidizing the graphite flake, which has first been subject to a purification step. Particles with resulting sizes >10 μm are converted to CSPG via surfacing coating, and have typical Cg purities of 99.95%+. The remaining particles, with sizes <10 μm will be sold as PMG materials, and have typical Cg purities of 98%+.
The Coosa PEA assumes a 27-year mine life (mining 10% of the mineral resource estimate and focused only on the oxidized top layer of material), and that production at Coosa will start at 5,000 t/year for five years, rising to 15,000 t/year by year 7. It is further assumed that the capital costs associated with such an expansion, are funded from the free cash flow produced in the initial production period. At an 8% discount rate, this results in a pre-tax Net Present Value (NPV) of $444M or $320M post-tax (all $ in USD), and an Internal Rate of Return of 52.2% pre-tax (45.7% post-tax).
I asked Mr. Baxter how these numbers would look if the expansion did not take place (i.e. if the 5,000 t/year production rate was constant throughout the life of the mine). Such a scenario results in an NPV of $157M pre-tax ($120M post-tax) at an 8% discount rate and an IRR of 47.8% pre-tax (42.4% post-tax).
The PEA assumes that CSPG can be sold for $9,000/t, with PMG fetching $2,000/t. These prices are based on estimates from Benchmark Mineral Intelligence of current selling prices of $7,000-12,000/t and $1,800-2,800/t for CSPG and PMG products respectively.
The PEA also states an estimated operating cost over the 27-year mine life of $1,555/t. This is a blended operating cost, covering the combined cost of production of CSPG and PMG. If accurate, these numbers would provide AGC with significant margins for its two product lines, particularly the CSPG material.
So on what basis does AGC believe that it can actually and economically produce these engineered graphite products? The company has been testing a number of processes for the purification, micronizing and spheroidizing of its graphite flake in recent months.
In September 2015, AGC announced that 99.99% Cg purities had been obtained across the full range of flake-size distributions. A conventional low-temperature thermal purification process, using chlorination, was applied by an unnamed metallurgical laboratory to graphite concentrates produced by SGS Mineral Services of Lakefield, Ontario. Recoveries of 90%+ following purification were obtained.
This announcement followed on the heels of the initiation of a pilot plant program at SGS, for the processing of a 200 t bulk sample into graphite concentrate. Mr. Edmondson said that the bulk sample came from a total of 10 pits, each providing approximately 20 t to the sample. The pits were evenly distributed across the Indicated mineral-resource area of the property, to represent the variations in grade, flake size and rock type typical to the deposit.
During my visit, Mr. Baxter indicated that tests of micronization and spheroidization processes for the purified Coosa graphite were underway. These processes were hinted at in the PEA report; a news release from the company issued in January 2016, detailed the results of downstream independent LIB tests using graphite anodes produced from Coosa CSPG materials.
The results announced in last month's news release indicate that AGC's micronizing, spheroidizing and coating processes were apparently successful. A tap density of 0.985 g/cm3 was achieved (anode production typically requires a minimum tap density of 0.9 g / cm3), along with a desirably low specific surface area, relative to the commercial LIBs tested.
A reversible capacity of 367.21 mAh/g and irreversible capacity loss of 5.09% were obtained for the AGC batteries, compared to 347.2 mAh/g and 6.06% respectively.
If these results can be replicated at the demo and subsequent commercial scales, AGC will have demonstrated the ability to effectively produce CSPG suitable for commercial-grade LIB graphite anodes.
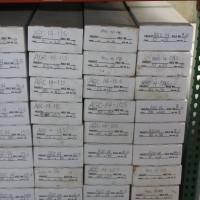
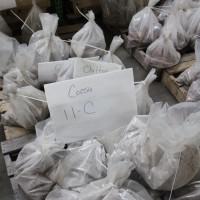
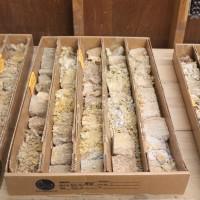
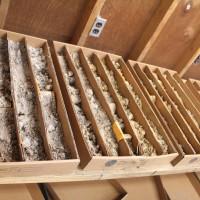
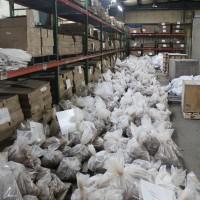
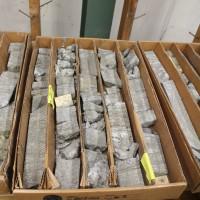
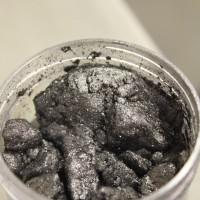
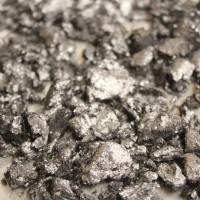
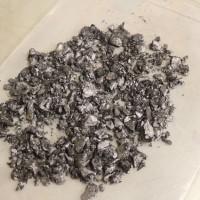
During my visit to Alabama, I asked Mr. Baxter about a couple of news releases issued by AGC earlier in the year, concerning the apparent occurrence of 'naturally occurring graphene' at the Coosa project site. He said that samples from the Coosa site had been analyzed at the University of Alabama, and graphene with 2-10 layers had been observed. Analysis was also performed at Queens University in Kingston, Ontario, which apparently observed the graphene layers in samples obtained from the rougher flotation process applied to bulk samples of Coosa materials.
Mr. Baxter described these initial findings (announced prior to his taking the helm at AGC last year) as "interesting but somewhat academic" at this stage. The presence of multi-layer graphene, if confirmed, may indicate that the graphite present at Coosa may be more susceptible to delamination, which if the case, would present the possibility of the use of shearing during processing. However, Mr. Baxter noted that AGC was firmly focused on the production of engineered graphite for battery and other applications, and not on graphene production. This was recently reiterated in AGC's January 2016 Corporate Update, confirming that AGC has no intentions of getting into "the graphene business."
Mr. Edmondson commented that because the Coosa project is located on private land, permitting for the project will rest at the state level, which should provide a relatively straightforward process when compared to mining projects on Federal or Crown land, elsewhere in North America. The company anticipates that the entire permitting process will require approximately six to eight months for completion. There is significant local and state-level support for the Coosa project, given the number of potential jobs that would be created from the project. The proximity to the Sylacauga marble mine means that there are significant numbers of skilled workers in the area; labor costs are relatively low in Alabama.
AGC is keen to stress its "Made in USA" credentials for a future Coosa mine; Mr. Baxter commented that the proximity of the project to current and future battery manufacturers in the USA, should give the company a key advantage in servicing such potential customers, over other projects located further afield. The company also highlights the Alabama connection on its website and presentations, tying in to the state's own "Made in Alabama" campaign and the apparent advantages that this might have.
Commenting on the future mine design for Coosa, Mr. Baxter said that a goal will be for zero discharge of wastes from the mine. The site will incorporate a number of sedimentation ponds and dry-stack tailings, where waste products will be stored after thickening. All water used for processing will be recycled, with small amounts of 'make-up' water used if needed.
The weather in Alabama is such that winterizing of buildings on the future mine and processing site will not be required.
The initial processing mill will be located on-site at the Coosa project. The plant for purification and further processing of the mined graphite will be located approximately 20 miles from Coosa in Rockford, Alabama, to which there is direct access from the Coosa site along county roads. An existing natural-gas pipeline runs through Rockford. The proximity of this pipeline will be beneficial to the capital and operational expenditures, associated with the furnaces needed for the processing facility in Rockford.
After visiting the Coosa project site, talking with AGC management and reviewing the recent announcements from the company concerning its battery-grade pilot-plant work, I believe that AGC's Coosa project is on a sound technical footing. The decision to go beyond the production of ROM graphite concentrate, in order to provide a 'one-stop shop' for its customers will serve the company well, if the price forecasts and actual operational costs are consistent with the PEA estimates. Combined with relatively modest initial production targets, AGC has a sensible and credible business model.
My thanks go to the AGC team for organizing the logistics of my visit, and to Don Baxter, Rick Keevil and Jesse Edmondson for hosting me during my time in Alabama.
Disclosure: at the time of writing, Gareth Hatch is neither a shareholder of, nor a consultant to, Alabama Graphite Corp (AGC). Neither he nor Technology Metals Research, LLC received compensation from AGC or from anyone else, in return for the writing of this article.