VANCOUVER, British Columbia, Feb. 25, 2019 (GLOBE NEWSWIRE) -- FPX Nickel
Corp. (FPX-TSX.V) (“FPX Nickel” or the “Company”) is pleased to announce
positive results from metallurgical testing on the Baptiste Deposit at its 100%-owned Decar Nickel District (the
“Project”) in central British Columbia. The metallurgical testing achieved meaningful improvements over the
results of previous metallurgical test work used as a basis for the Project’s 2013 preliminary economic assessment (“2013
PEA”), demonstrating significant increases in estimated nickel recovery and final concentrate quality, using conventional
processing technologies.
Highlights
- Conventional flowsheet based on grinding, magnetic separation and flotation processes
- Consistent production of nickel (“Ni”) concentrates with improvements in grade and recovery, versus 2013 PEA
projections, as shown in Table 1 below
- Consistent production of iron ore concentrates grading up to 64% iron (“Fe”) content, the first successful
generation of a potentially commercial by-product in the Project’s testing history
A comparison of the results of the 2019 metallurgical test program with the assumptions in the 2013 PEA is provided in Table
1.
Table 1 – Summary of Metallurgical Improvements
Metallurgical Parameter |
Metallurgical
Assumptions in
2013 PEA |
Results of 2019
Metallurgical Test
Program |
Nickel Concentrate Grade |
13.5% Ni |
55-72% Ni |
Davis Tube Recoverable (“DTR”) Nickel Recovery |
82% |
80-90% |
Iron Ore Concentrate Grade |
N/A |
58-64% Fe |
“These metallurgical results confirm an important technical breakthrough for the Decar Project,” commented Martin Turenne, the
Company’s President and CEO. “The confirmation of a simple, robust flowsheet using conventional magnetic separation and flotation
parameters paves the way for Decar’s ongoing development, and for the exploration and development of awaruite nickel targets
generally. The substantial increase in projected DTR nickel recoveries from 82% in the 2013 PEA to up to 90% demonstrates the
strong metallurgical performance of the Baptiste deposit. The consistent production of concentrates grading from 55% to 72%
nickel further establishes the potential for the Baptiste deposit to generate a clean nickel product with no sulphur and very high
metal content.”
Mr. Turenne continued, “We also note the successful production of a high iron-content by-product, which provides the basis to
investigate the potential implications of an entirely new product stream on the Project’s economics. We will continue to
advance this metallurgical program through further optimization testing and trade-off studies to optimize the components of an
updated mine plan for the Baptiste Deposit.”
Description of Metallurgical Test Work
The metallurgical testing was conducted at ALS Metallurgy in Kamloops, British Columbia and overseen by Jeffrey B. Austin, P.
Eng., President of International Metallurgical and Environmental Inc. The test work was completed on a representative
mineralized composite measuring approximately 400 kilograms comprised of core sample reject material from four drill holes
completed in 2012 and 2017 in the southeastern portion of the Baptiste Deposit.
The metallurgical study consisted of two phases of testing. Phase 1 was focused primarily on magnetic separation of
magnetic materials from non-magnetic materials in the composite material. Approximately 75 percent of the contained nickel in
the Baptiste Deposit occurs as awaruite, a highly magnetic nickel-iron alloy that is readily recovered by low-intensity magnetic
separation. The deposit also contains significant magnetite (iron oxide), which is recovered concurrently with the awaruite
in magnetic separation. Phase 1 test work confirmed the recovery of nickel and iron using magnetic separation and the
upgrading of these minerals into a bulk Ni-Fe concentrate using re-grinding and magnetic cleaning.
Phase 2 involved flotation tests on magnetic concentrates produced in Phase 1 to enable the separation of awaruite from
magnetite for the production of two concentrates: a nickel concentrate grading from 55% to 72% Ni and 25% Fe, and a magnetite iron
ore concentrate grading from 58% to 64% Fe. The high-grade nickel concentrate produced during the testing program
approximates the composition of pure awaruite, a nickel-iron alloy comprised of approximately 75% Ni and 25% Fe.
Phase 2 testing confirmed that the separation of nickel from a bulk Ni-Fe concentrate can be achieved using traditional
flotation processes. Test work at ALS included open circuit testing of nickel recovery to evaluate reagent options,
liberation requirements in flotation, and retention time requirements. The flotation process uses copper sulphate to
facilitate the attachment of flotation collectors to the awaruite mineral surface in a manner that mirrors conventional zinc
flotation processes. Flotation collector 3418A, an industry standard reagent, was used in the flotation process.
The tailings stream from the nickel flotation process is a high-grade iron concentrate which testing has shown to contain 58 to
64% iron. The Company plans further evaluative work to examine the commercial potential of this iron ore concentrate,
including an evaluation of the possible impact on the Project’s economics.
In summary, the production of a 55% to 72% nickel concentrate and an iron ore concentrate grading 58 to 64% Fe from the Baptiste
composite sample with a feed grade of 0.145% DTR Ni is based on traditional grinding, magnetic separation and flotation processes;
a flowsheet is shown in Figure 1. Unit operations in this flowsheet include crushing, grinding to 120-360 microns
(P80), magnetic separation with a mass pull of 10-15%, magnetic concentrate re-grinding to 25 microns (P80),
rougher flotation concentrate production and flotation cleaning.
Figure 1 – Proposed Flowsheet for Baptiste Nickel Recovery and Upgrading is available at http://www.globenewswire.com/NewsRoom/AttachmentNg/486cbebe-7f0f-4658-bd5b-36fb88bbdffa
The expected metallurgical performance of the test sample, based on test work completed at ALS Metallurgy, is summarized in
Table 2.
Table 2 – Summary of Expected Metallurgical Performance – Baptiste Composite Sample
Primary Grind Size
(P80 microns) |
Mass Recovered to Magnetic
Rough Concentrate (Note 1) |
Overall Process Recovery
(% of DTR Ni Feed Grade) |
90 |
10% |
90% |
120 |
10% |
89% |
240 |
15% |
84% |
360 |
15% |
80% |
Note 1: Mass Recovered to Magnetic Rough Concentrate: weight percentage of the magnetic concentrate, relative
to the weight of the feed to the magnetic separator
These results were obtained with a consistent set of metallurgical parameters across all test samples and demonstrate a
significant improvement over test work completed for the 2013 PEA, demonstrating higher nickel recoveries, higher nickel grade in
the final concentrate and a lower mass pull in magnetic separation. The recovery and concentrate grade assumptions in the
2013 PEA were based on a two-stage process consisting of a primary coarse grind to P80 600 microns, followed by rougher
magnetic separation with an estimated mass pull of 33%, then a re-grind of that fraction to P80 70 microns followed by
Knelson gravity concentration to produce a concentrate grading 13.5% nickel, 45-50% iron and 1-2% chromium. The projected
recoveries in the 2013 PEA were 82% of the DTR nickel (see 2013 PEA filed under the Company’s SEDAR profile on August 21,
2013).
Future Metallurgical Test Work
The Company will undertake further metallurgical test work in 2019 to evaluate the following aspects of metallurgical
performance:
- Optimization of the flotation process for the production of high-grade nickel concentrates, including evaluation of reagent
quantities and locked-cycle test performance
- Optimization of the quality of the iron ore concentrate produced as a by-product of the nickel recovery process
- Detailed evaluation of minor elements in the nickel concentrate and iron ore concentrate
- Leach testing to evaluate the amenability of magnetic and flotation concentrates to the production of a high-grade nickel
solution
Cautionary Note Regarding 2013 PEA
The 2013 PEA, by definition, is preliminary in nature and includes inferred mineral resources that are considered too
speculative geologically to have economic considerations applied to them that would enable them to be categorized as mineral
reserves. There can be no certainty that the PEA will be realized. It is important to note that mineral resources are
not mineral reserves and do not have demonstrated economic viability.
Qualified Persons
The metallurgical information in this news release has been prepared in accordance with Canadian regulatory requirements set out
in National Instrument 43-101 Standards of Disclosures for Minerals Projects of the Canadian Securities Administrators (“NI
43-101”) and supervised, reviewed and verified by Jeffrey B. Austin, P.Eng., President of International Metallurgical and
Environmental Inc., a “Qualified Person” as defined by NI 43-101 and the person who oversees metallurgical developments for FPX
Nickel.
About the Decar Nickel District
The Company’s Decar Nickel District claims cover 245 square kilometres of the Mount Sidney Williams ultramafic/ophiolite
complex, 90 km northwest of Fort St. James in central BC. The District is a two hour drive from Fort St. James on a high-speed
logging road. A branch line of the Canadian National Railway is less than 5 kilometres east from Decar’s Baptiste Deposit and
the BC Hydro power grid comes within 110 kilometres south of the property.
Decar hosts a greenfield discovery of nickel mineralization in the form of a naturally occurring nickel-iron alloy called
awaruite, which is amenable to bulk-tonnage, open-pit mining. Awaruite mineralization has been identified in four target areas
within this ophiolite complex, being the Baptiste Deposit, the B Target, the Sid Target and Van Target, as confirmed by drilling in
the first three plus petrographic examination, electron probe analyses and outcrop sampling on all four.
Of the four targets in the Decar Nickel District, the Baptiste Deposit has been the main focus of diamond drilling from 2010 to
2017, with a total of 82 holes completed. The Sid Target was tested with two holes in 2010 and the B Target had a single hole
drilled into it in 2011; all three holes intersected nickel-iron alloy mineralization over wide intervals with DTR nickel grades
comparable to the Baptiste Deposit. The Van Target was not drill-tested at that time as rock exposure was very poor prior to
logging activity by forestry companies.
As reported in a NI 43-101 resource estimate prepared on February 26, 2018, the Baptiste deposit contains 1.843 billion tonnes
of indicated resources at an average grade of 0.123% DTR nickel, for 2.3 million tonnes of DTR nickel, and 391 million tonnes of
inferred resources with an average grade of 0.115% DTR nickel, for 0.4 million tonnes of DTR nickel, reported at a cut-off grade of
0.06%. Mineral resources are not mineral reserves and do not have demonstrated economic viability.
About FPX Nickel Corp.
FPX Nickel Corp. is focused on the exploration and development of the Decar Nickel-Iron Alloy Project, located in central
British Columbia, and other occurrences of the same unique style of naturally occurring nickel-iron alloy mineralization known as
awaruite. For more information, please view the Company’s website at www.fpxnickel.com or contact Martin Turenne, President and CEO, at (604) 681-8600.
On behalf of FPX Nickel Corp.
"Martin Turenne"
Martin Turenne, President, CEO and Director
Forward-Looking Statements
Certain of the statements made and information contained herein is considered “forward-looking information” within the
meaning of applicable Canadian securities laws. These statements address future events and conditions and so involve inherent risks
and uncertainties, as disclosed in the Company's periodic filings with Canadian securities regulators. Actual results could differ
from those currently projected. The Company does not assume the obligation to update any forward-looking statement.
Neither the TSX Venture Exchange nor its Regulation Services Provider accepts responsibility for the adequacy or accuracy of
this release.
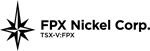
Figure 1
Proposed Flowsheet for Baptiste Nickel Recovery and Upgrading