Tech Talk: The THAI process for bitumen and heavy oil
http://www.theoildrum.com/node/6183
Posted by Heading Out on February 7, 2010 - 9:14am
Topic: Supply/Production
Tags: bitumen, heavy oil, tech talk, toe to heel air injection [list all tags]
For a while, when I was a student, I had an attic bedroom that washeated by a small coal fire, with a relatively short chimney up to theroof. I learned, fairly early on, that in starting the fire you neededa fairly high velocity air flow across the coals, and underlyingfirewood strips. And to get this I would rest a shovel over the frontof the fireplace, and try and seal off the sides. I kept a smallbellows beside the fire to help when this wasn’t particularlysuccessful. When you are starting a fire underground the provision ofair is critical, but when you are trying to burn the residual coke thatis left, after the heat has cracked the rest of the oil and caused itto flow away, keeping that air flowing at a high enough rate to sustainthe high-temperature burn becomes somewhat critical to most efficientoperation, particularly if the air has to get through a sand layer toreach the fire.
This is the post on THAI – Toe to Heel Air Injection for therecovery of heavy oils, which is part of the ongoing technical post (tech talk)series that I write on Sundays. It is a subject that has been describedseveral times in the past at The Oil Drum. I first mentioned it back in 2006 when the first underground test was underway at White Sands.
I used this illustration at the time.
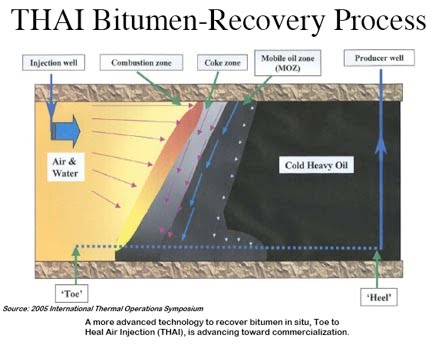
It is an artist’s impression of a side view of the site, with the bluedotted horizontal line representing the recovery well and air being fedin from a higher well into the formation. The test at White Sands inAlberta has been followed by a
test at Lloydminster in Saskatchewan which got underway in a more conventional heavy oil last October.
The Kerrobert project followed much on the procedures from the earlier test, and the currently planned full scale production at May River (Large pdf file)
Petrobank, which is partnered with Baytex Energy Truston the 50/50 joint venture, recently sunk two vertical air-injectionwells and two horizontal production wells into the extensive Mannvilleconventional oil reservoir near Kerrobert.
Compressed air was added last week after a temporary steaming of theground to mobilize the oil around the injector site. With the additionof the air, spontaneous underground combustion has begun.
"I think we will see some oil as early as today," Bloomer said.
Don and Gail described the THAI process in 2007 and have given some history on its use, THAI having been patented by Petrobank who have a 12 minute video on the process and the first trial and preparation for full scale production. It is well worth watching.
Dave Murphy had an update on the EROI costs in March of last year.
While watching the video is the best way to understand the process,it can also be illustrated with a picture from the plan for May Riverand I will lift some parts of that document to describe what is plannedfor that site.
Illustration of the key parts of the process.The horizontal wells are drilled (a suite of eighteen wells, eachwith a 2,000 ft horizontal section, spaced 410 ft apart) some 7 ftabove the bottom of the formation (or the water table if that becomesan issue). Above these the air injection wells are drilleddirectionally and offset from the toe of the well. (By usingdirectional drilling air injection can be better controlled than withthe original vertical wells).
Layout of the air injection (upper) and production wells.Once the wells are in position steam will be injected and circulatedfor a period of 3 months to bring the sand and bitumen up to around 100deg C, then air will be injected to start combustion. The part of thebitumen that burns as the process develops is the residual asphaltenethat is left after the lighter fractions are either evaporated, flowaway at reduced viscocity or are cracked by the high temperature (>400 deg C). The residual material, apparently about 10% of the OOIP,provides the fuel, driving some 90% of the fuel into the productionwell.
To sustain production after ignition and flame front stabilizationhas occurred, the wells will carry some 4.4 million cf/day into theformation, and about the same amount of a mix of carbon monoxide,carbon dioxide, and hydrocarbon gas will be released. As the videonotes that gas will be used on site to generate electricity to run theair compressors, and to provide site power. Based on the earlier teststhe site is anticipated to generate some 10,000 bd of cracked bitumen,and about twice that in water production. The flame front will moveforward at between 5 and 10 inches a day. The oil is projected to be asignificant upgrade of the original bitumen. The water has thepotential for being sold to other operators in the area for use in SAGDproduction.
Comparison of bitumen with THAI produced oil.The energy efficiency of the site is anticipated to be 85.7%. Itshould be noted that the document I have taken this information fromalso contains a conservation and reclamation plan. (But at 653 pageslong for the whole document I have only noted key passages for thetheme of the post).
In response to my SAGD post both Rockman and RockyMtnGuy commented about using underground combustion to help with getting the bitumen from the oil sand.
One of the things that they were concerned about, as was I, is thecontrol of the flame front which becomes more difficult as the heightof the production zone is around 70 ft. However at May River they planon burning from the outside in, so this may control the extent to whichthe fire overburns. In addition, as I noted at the beginning of thepost, it is rather difficult sometimes to sustain the righttemperatures without a high flow of air, and that may provide a furthercontrol.
The conditions are somewhat different at Kerrobert where the oil isless viscous and the formation is around 100 ft thick. This has caused some problems since the well flows exceeded what had been anticipated:
the original plan was to use temporary hydraulic pumpson each well to create a drawdown pressure across the horizontal welland, as combustion gas production increased, pumping would cease andwells would flow by produced gas lift.
Initial fluid production volumes were tested at 180 to 300 barrelsper day per well, with oil cuts ranging from zero to 40%. However,during the transition phase to gas lift it was learned that liquidinflow to the production wells exceeded the pump's capacity, whichlimited the ability to draw down the wells and caused frequent pumpfailures. On Dec. 21, the pump in KP1 was re-configured to improve itspumping capacity. Now KP2 is being re-configured and is expected to beproducing at similar rates to KP1 within the next few days.
Since the re-configuration, fluid production rates from KP1 haveranged between 250 and 420 bbls per day with oil cuts averaging 36% andreaching as high as 65%. Also, the air injection rate was increased to50,000 cubic metres per day and the produced gas rate has increased to8,000 cubic metres per day.
Looks as though things are going quite well.
Oh, and the disadvantage of having a small coal fire in a garretflat is that during the night it went out, and in the morning I wouldoccasionally wake up with snow in the grate.